蜗轮蜗杆传动效率优化方法
蜗轮蜗杆传动因其结构紧凑、传动比大等优点在许多机械设备中得到广泛应用,但其传动效率较低一直是亟待解决的问题。以下是一些有效的优化方法:
1. 提高制造精度
- 蜗轮和蜗杆的制造精度:制造精度对减速器的传动效率影响较大。精度越高,传动效率越高。高精度的蜗轮和蜗杆可以减少摩擦损失和啮合损失,从而提高传动效率。
2. 改善表面粗糙度
- 表面粗糙度:蜗轮和蜗杆表面的粗糙度也会影响减速器的传动效率。表面越光滑,传动效率越高。通过采用高精度的加工技术和表面处理工艺,可以显著降低表面粗糙度。
3. 优化润滑方式
- 油润滑:通过定期添加润滑油或油雾润滑,可以降低摩擦和磨损,提高传动效率和使用寿命。润滑油的选择应考虑工作环境和工况,选择合适的黏度和添加剂。
- 脂润滑:对于某些应用场景,可以使用润滑脂来润滑蜗轮蜗杆,其优点是使用简便、不易流失。但需要定期补充或更换润滑脂。
- 特殊润滑:对于高温、高负荷等特殊应用场景,可能需要采用特殊的润滑方式,如固体润滑剂或气体润滑。
4. 增加蜗杆头数
- 增加蜗杆头数:这是提高蜗杆传动效率的最有效的方法之一。增加蜗杆头数可以减少单个齿的负载,降低摩擦损失,从而提高传动效率。
5. 减小空隙
- 减小空隙:蜗轮蜗杆传动中,由于制造精度和装配误差,齿面之间存在一定的空隙。在传动过程中,这些空隙会导致齿与齿之间的碰撞,产生额外的能量损失。通过提高制造和装配精度,可以减小这些空隙,提高传动效率。
6. 降低滑动损失
- 降低滑动损失:蜗轮蜗杆传动中,由于蜗杆的螺旋升角和蜗轮的螺旋降角,蜗轮蜗杆之间存在一定的相对滑动。这种滑动会导致能量损失,降低传动效率。通过优化设计,减小滑动距离,可以降低滑动损失。
7. 合理选型和维护
- 合理选型:选择合适的蜗轮蜗杆型号和参数,以满足实际工况的需求,避免过大的能量损失。
- 定期维护:根据实际情况,制定合理的预防性维护计划,包括定期更换易损件、清洗和检查等,以延长蜗轮蜗杆的使用寿命。
总结
蜗轮蜗杆传动效率的优化是一个系统工程,需要从多个方面进行综合考虑和改进。通过提高制造精度、改善表面粗糙度、优化润滑方式、增加蜗杆头数、减小空隙、降低滑动损失以及合理选型和维护,可以显著提高蜗轮蜗杆传动的效率,延长其使用寿命,提高机械设备的整体性能。
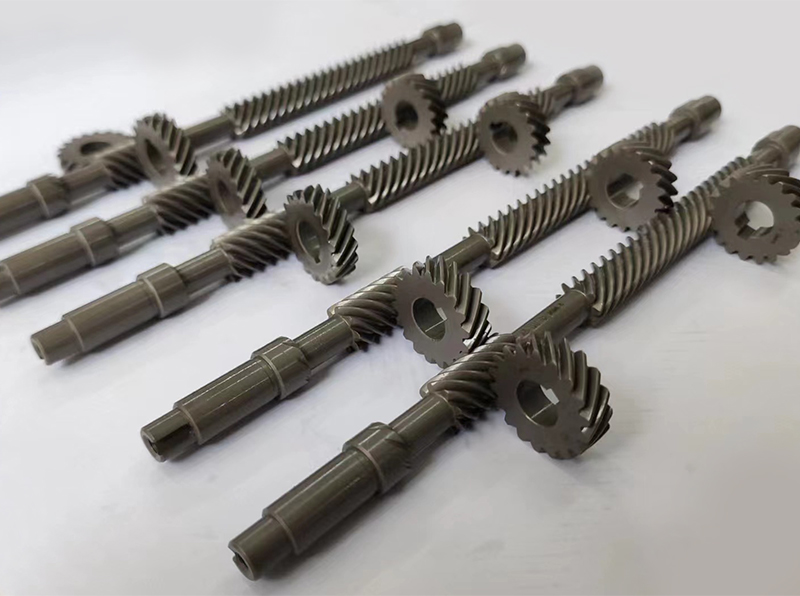
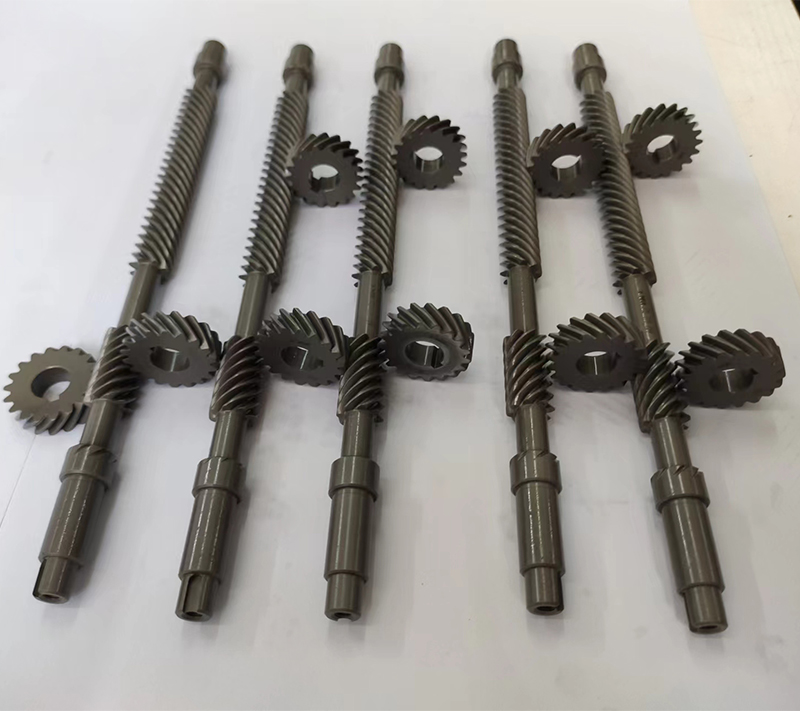