蜗轮蜗杆传动比优化策略
蜗轮蜗杆传动因其独特的优点,如大传动比、结构紧凑和自锁性,在许多机械设备中得到广泛应用。然而,为了提高传动效率和延长使用寿命,需要对传动比进行优化。以下是几种常见的优化策略:
1. 选择合适的蜗杆头数和蜗轮齿数
- 蜗轮齿数应根据所需的传动比和实际工况来选择。通常,蜗轮齿数越多,传动比越大,但制造成本和复杂性也会增加。
2. 提高传动效率
- 使用高效润滑剂:选择合适的润滑剂可以显著减少蜗轮蜗杆之间的摩擦损失,提高传动效率。
- 优化材料选择:选择具有良好减摩、耐磨和抗胶合性能的材料,如高强度青铜或特殊合金,可以减少磨损和胶合现象。
3. 提高承载能力
- 多齿啮合:通过增加蜗轮的齿数和蜗杆的头数,可以增加同时啮合的齿数,提高承载能力。
- 模数选择:合理选择模数,可以平衡传动比和承载能力。模数越大,承载能力越强,但体积和重量也会增加。
- 中心距调整:适当调整中心距,可以优化传动性能,减少应力集中。
4. 减少噪声和振动
- 降低蜗杆的转速:通过降低蜗杆的转速,可以减少噪声和振动,提高传动的平稳性。
- 高精度加工:确保蜗轮和蜗杆的齿形精度,可以减少啮合时的冲击和噪声。
- 非金属材料:使用非金属材料制作蜗轮,可以有效降低噪声,提高传动的平稳性。
5. 考虑自锁性
- 自锁性:蜗轮蜗杆传动具有自锁性,即当蜗杆停止转动时,蜗轮不能反向驱动蜗杆。这一特性在某些应用中非常有用,如起重机械中的安全保护。
- 避免过度依赖:虽然自锁性可以提供安全保护,但在某些情况下,过度依赖自锁性可能导致系统响应迟缓。因此,需要在设计时综合考虑自锁性和其他性能指标。
最后, 通过对蜗杆头数和蜗轮齿数的合理选择,提高传动效率,优化设计参数,减少噪声和振动,以及充分利用自锁特性,可以有效优化蜗轮蜗杆传动比,提高系统的整体性能和可靠性。
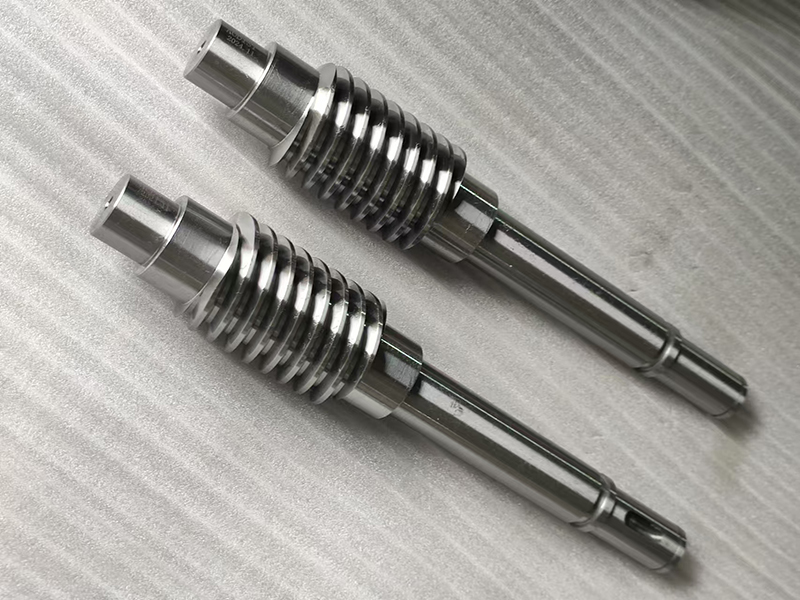
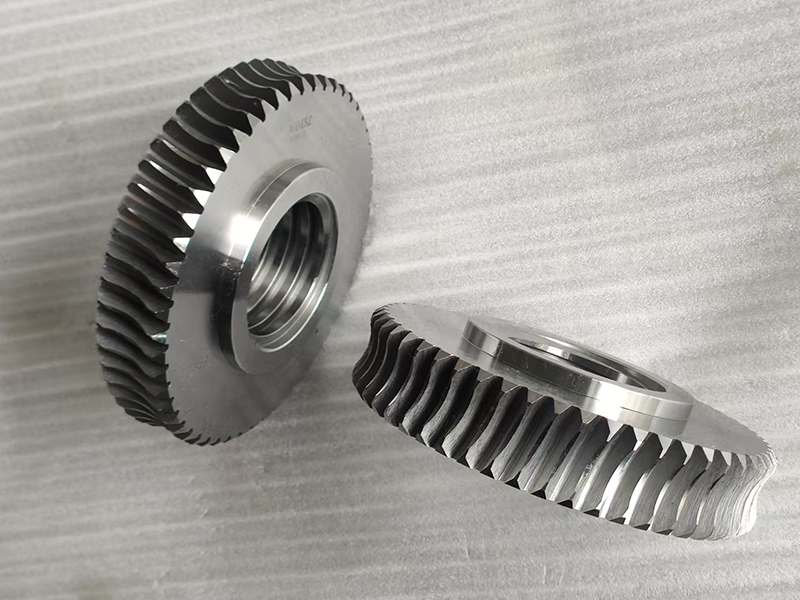